It was anything but a slow start. Krones launched its first filler in 1974. And just a short twelve months later, Hermann Kronseder revolutionised the traditional bottling line by presenting the sector with a drastic makeover: the block layout, which means mechanically linking up several machines without conveyors between them. Block technology has remained a defining element for our company, which is why we shall next year dedicate a special article to its 50th anniversary. For the time being, we focus on traditional filling technology here. The advances made in this area were impressive, to say the least: The first fillers were already rated at a few tens of thousands of containers per hour. A leaflet published in September 1977 specified an hourly output of 50,000 bottles for an early Krones block.
In 1974, the Krones company was 23 years old and a leader in labelling technology, with a number of patents to prove it. That was fifty years ago, and in that year Hermann Kronseder displayed admirable foresight by diversifying his business. Within a mere twelve months, he brought both a filler and a bottle washer to market. And it did not take him long to set new standards here as well, as anyone taking a look at the development of filling technology will swiftly realise.
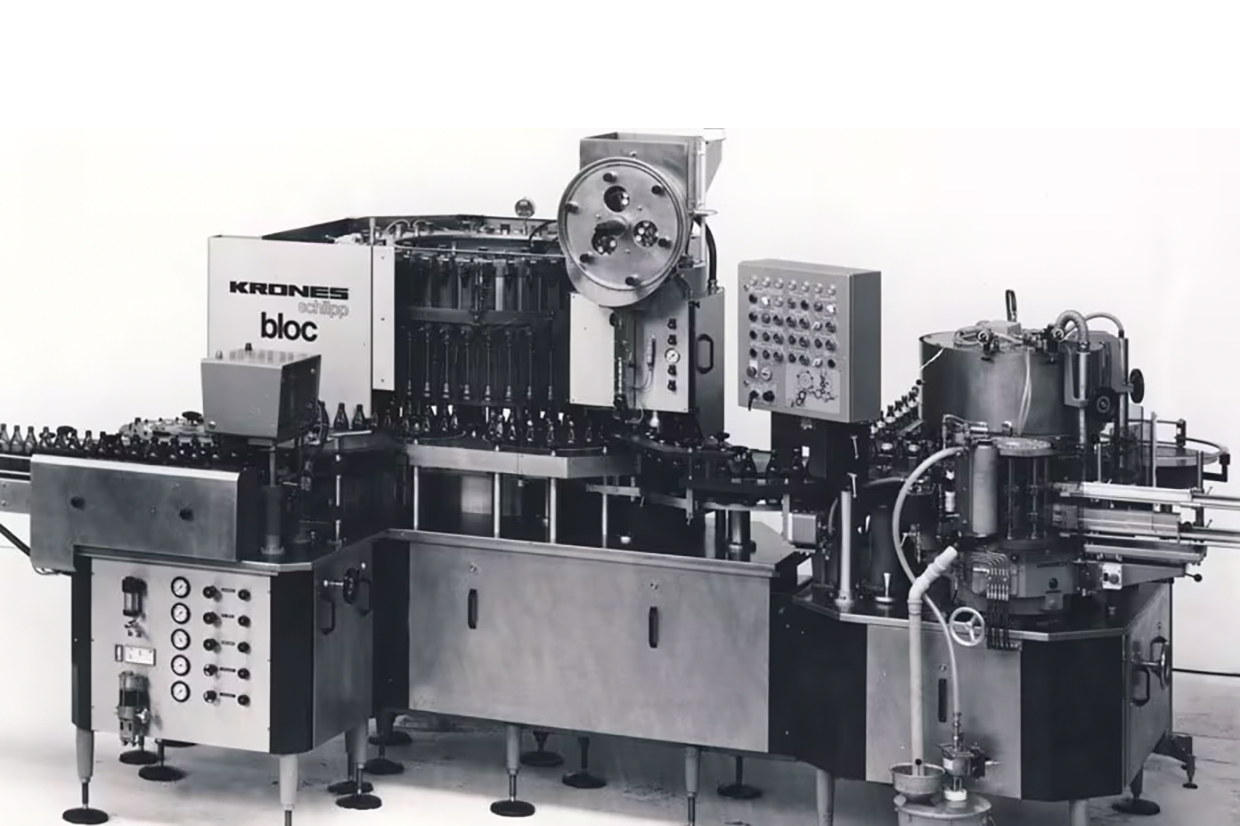
Right up into the 1980s, it was mainly beer and flavoured carbonated soft drinks that were filled mostly into glass bottles – in Europe, at least. These drinks were complemented by juices, wine, spirits and mineral water. Mind you, demand for the latter was then not as broadly based as it is today. At that time, cans were already a popular choice in the USA because these not so heavy, disposable containers, once pasteurised, were ideal for long-distance overland transport by train and truck. Krones responded to that demand by launching its own can filler on the market in 1989. Its first models still featured only mechanically controlled filling valves and vent tubes.
Best-seller: the volumetric can filler
In 1993, Krones gained a lead over its competitors by developing the volumetric VOC can filler. What set this new machine apart was its method of determining the fill quantity. Instead of using measuring probes or vent tubes for adjusting the fill level in the can, the VOC featured a high-precision metering chamber with an integrated float for filling exactly the right quantity of product into the can. Thanks to this unique selling point, the machine quickly turned into a best-seller and remained a huge success for many years after. This design featuring a metering chamber was initially also offered for bottles (VO filler) but was then replaced by a flow-meter system some time later.
In 1995, Krones built what was at the time the world’s biggest can filler with a carousel diameter of six metres and rated at 120,000 cans per hour. Three of these giant machines went to South America.
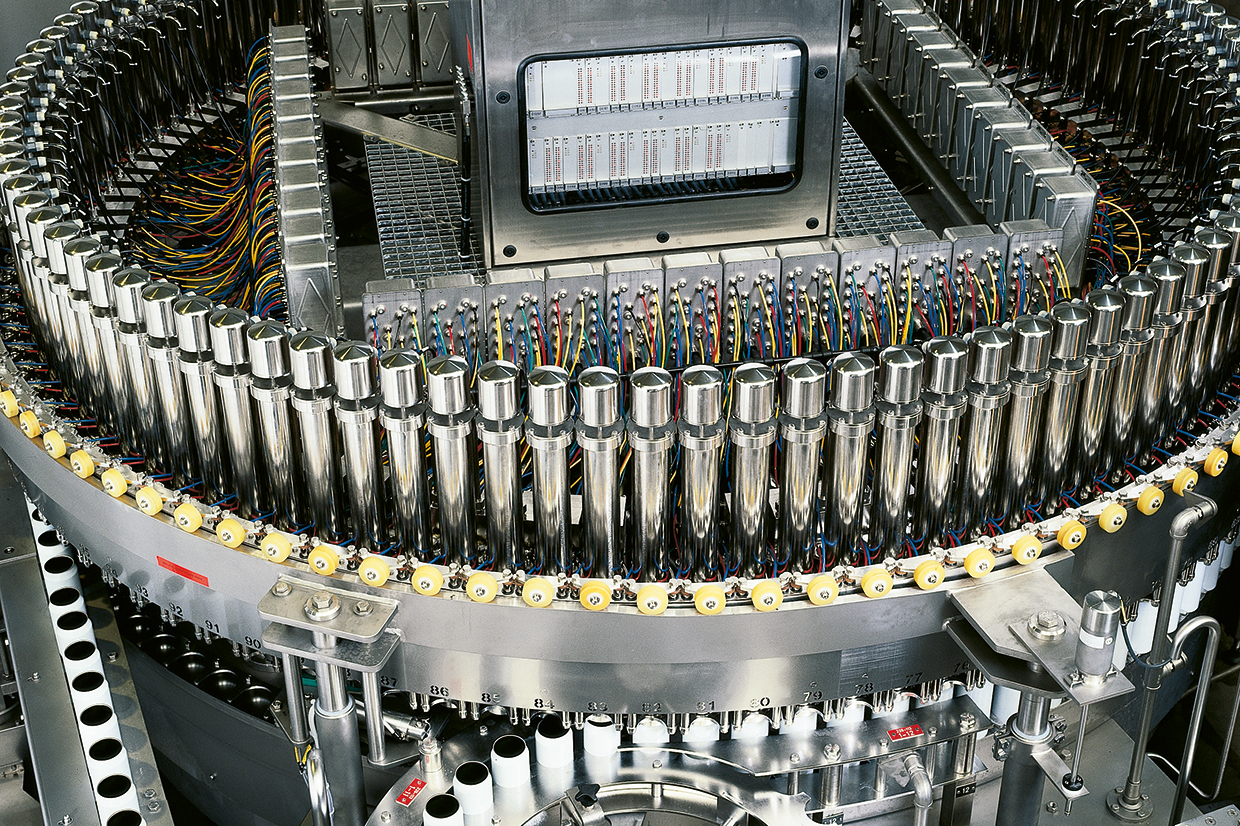
Newcomer: the PET bottle
But let’s go back a little in the timeline and have a look at a second type of container: Curtain up for the PET bottle! 1987 saw Krones start development work on a technology for filling PET containers, which just like any other type of bottle have their own idiosyncrasy. They are susceptible to scuffing, meaning scratch rings on their surface caused by the bottles rubbing against each other on the conveyor belt. To prevent them from touching each other as far as possible, the design team worked out a neck-handling system for the filler carousel. The first PET filler did not feature lift cylinders like a glass filler but instead one vertically adjustable slide at the ring bowl for every filling valve. Each of these slides had a support sheet with a U-shaped recess at its bottom end, which in the infeed starwheel moved to a position below the neck ring of the bottle to pick it up. The bottle was then lifted up to the filling valve and locked in place for a gastight seal. This approach offered another crucial advantage: Apart from very few exceptions, most PET bottles have the same mouth diameter, so no modifications were needed when changing over to a different bottle.
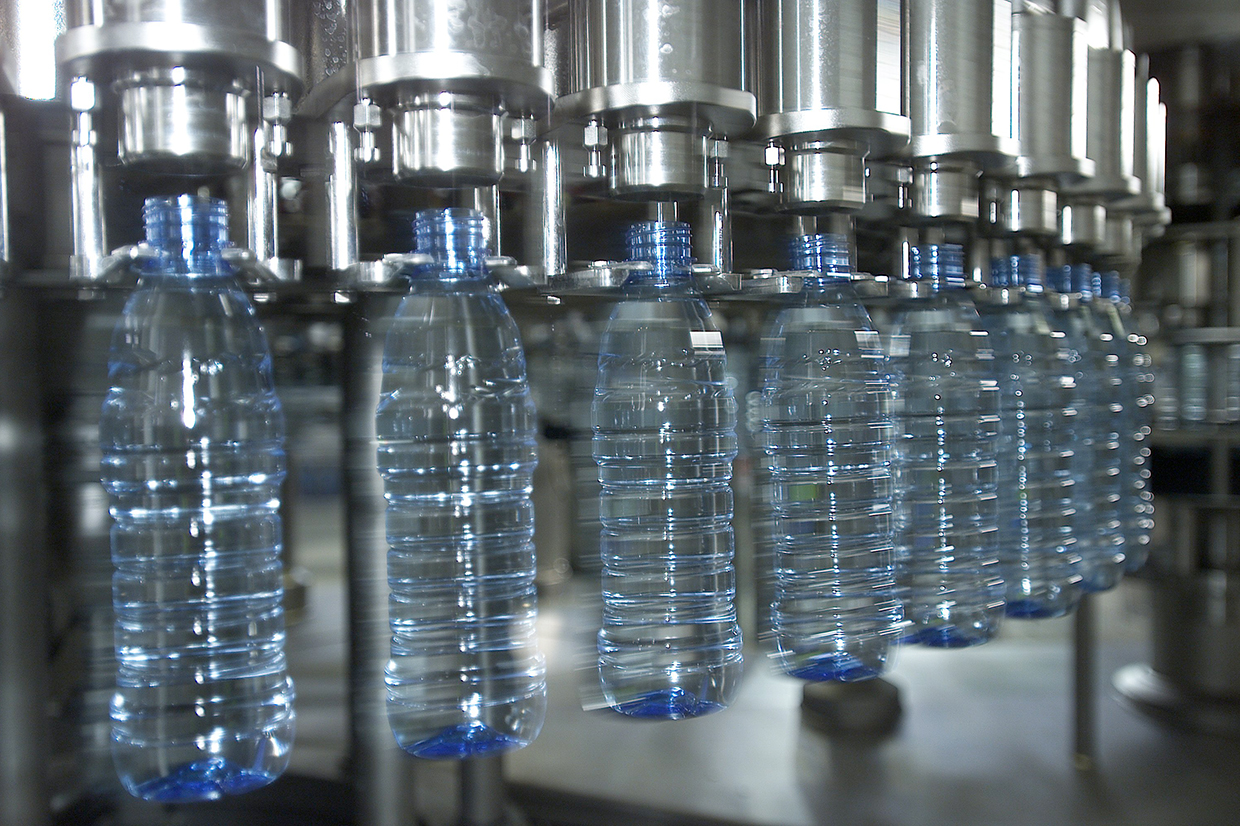
At the 1989 Interbrau in Munich, this concept was presented together with a third-party stretch blow-moulder running inline, just upstream. Back then, the bottles were taken to the new PET filler freely suspended in an air conveyor. “In developing this concept, Krones revolutionised line technology and competitors had to follow suit,” says Matthias Wahl.
Development work on controllable clamps started in 1995. Taking the body clamps for glass bottles as the basis, controllable neck grippers for PET bottles with neck ring were created in the next step. That enabled all machine starwheels to be fitted with them, which meant bottle guides at the starwheels were no longer required. In 1997, Krones unveiled its scuffing-free neck-handling system for PET, in the PET Superbloc, consisting of rinser, filler and capper. In 2009, the company then opted to go all-in with block technology and introduced the ErgoBloc L. That configuration featured neck-handling throughout, from the blow-moulder and labeller right through to the filler and capper, thus obviating the need for air conveyors.
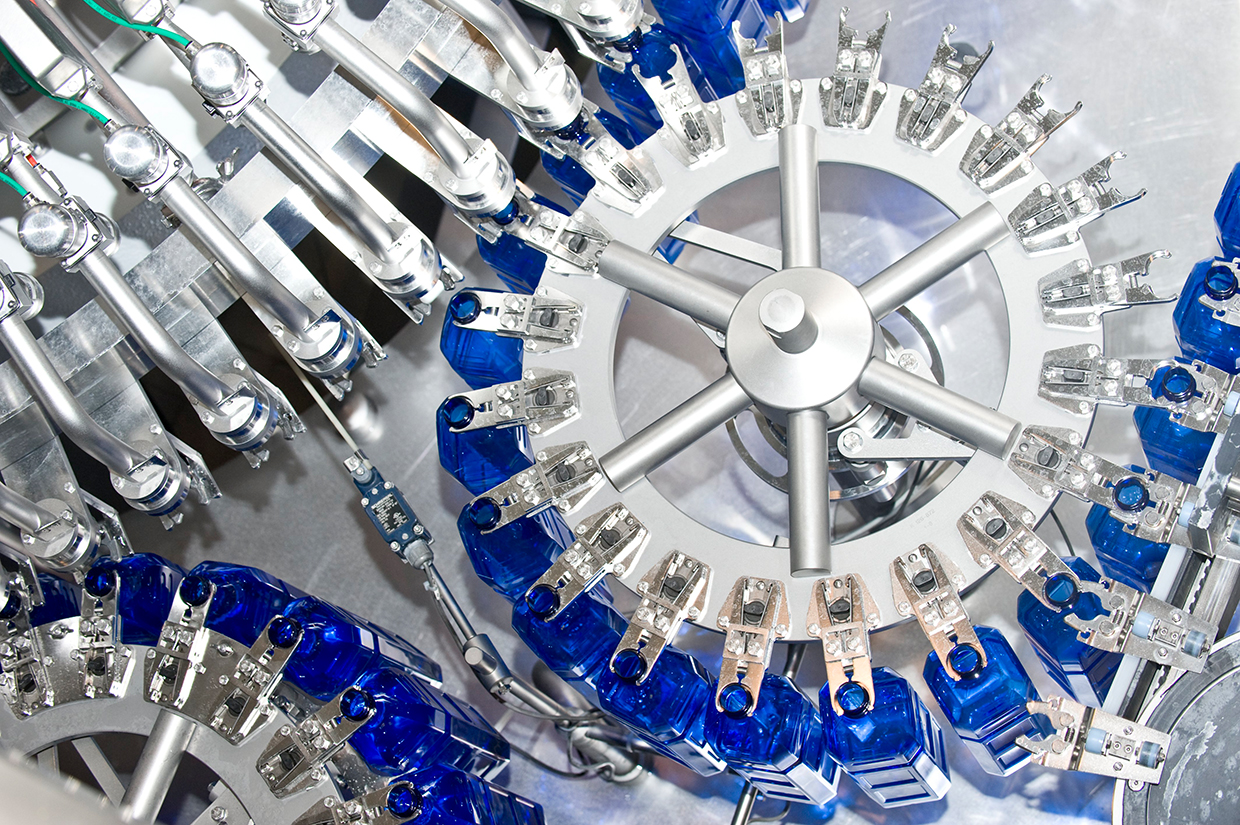
Electronics in filling technology
After this digression into the world of PET bottles and cans, let’s return to the development of filling technology in general and take a special look at the functional principle involved. Right up to the late 1980s, Krones’ fillers were controlled by mechanical means only, with cam controls on the outside of the filler’s carousel actuating the valves. That means the flow velocity was determined solely by the mechanical design, and operators were not able to simply switch to another type of beverage by modifying the filling parameters. This was not possible until filling concepts with central valve control were developed. Krones implemented this new idea in its VP filling system and launched its first electro-pneumatic filler in 1991. The valves were actuated pneumatically, with the compressed air needed to do this under central electric control. At that time, the design engineers did not yet dare use electronics directly at the valves located in the filler’s wet area.
Krones also introduced probes in the filling valves for electronic control of the fill level. For the first time, it was possible to use software to control the exact filling time independently of the current filler speed and to optimally adjust the process parameters. “The filling system, which was later on named Sensometic, was a crucial step forward for Krones,” says Matthias Wahl.
Entering the field of sterile filling
Based on these electro-pneumatic valves, Krones built its first machine for sterile beer filling in 1992, which flushed the bottles with steam prior to filling in order to sterilise them. The solution was aimed at breweries that wanted to improve the shelf life of their beers but didn’t like to pasteurise them because thermal treatment might affect their taste. The filler for sterile beer filling also marked Krones’ debut in aseptic beverage filling (see box).
In the 1990s, sales figures for fillers were rocketing: Krones supplied its 500th filler to a Bavarian brewery in 1990. A mere three years later, the 1,000th machine, a volumetric can filler, went on its way to Ireland. And in 2000, Krones received the order for the 2,000th filler.
Hygienic design and integrated electronics
One example for simple yet highly effective hygienic design is the hipped-roof tabletop in conjunction with free-standing machine guarding, with which Krones has set a new trend starting in 2000. Up till then, filler tables had been flat, so it was possible for beverage residues and glass fragments to collect on them, thus jeopardising line hygiene. By contrast, as its name implies, all four sides of the hipped-roof tabletop slope downward from the peak, ensuring that liquids flow down and glass fragments slide down. Sloping surfaces of that kind are nowadays standard in hygienic filling concepts.
Five years later, Krones did away entirely with a table in its F1 PET filler, enabling beverage residues and cleaning agents to flow away freely. A filler without a table? That was only made possible by way of electronic synchronisation of separate electric drives for the filler carousel and the starwheels. Up till then, synchronisation had been provided mechanically by gearwheels located under the table, which protected them. In the F1, by contrast, each starwheel was installed on a Monotec column, which housed its own separate motor. The control electronics of this filler were also integrated near the filling valves – meaning in the wet area – for the first time. “The F1 filler presented at the drinktec 2005 was a trail-blazing concept that was subsequently taken as a reference point by many competitors to a greater or lesser extent,” explains Matthias Wahl.
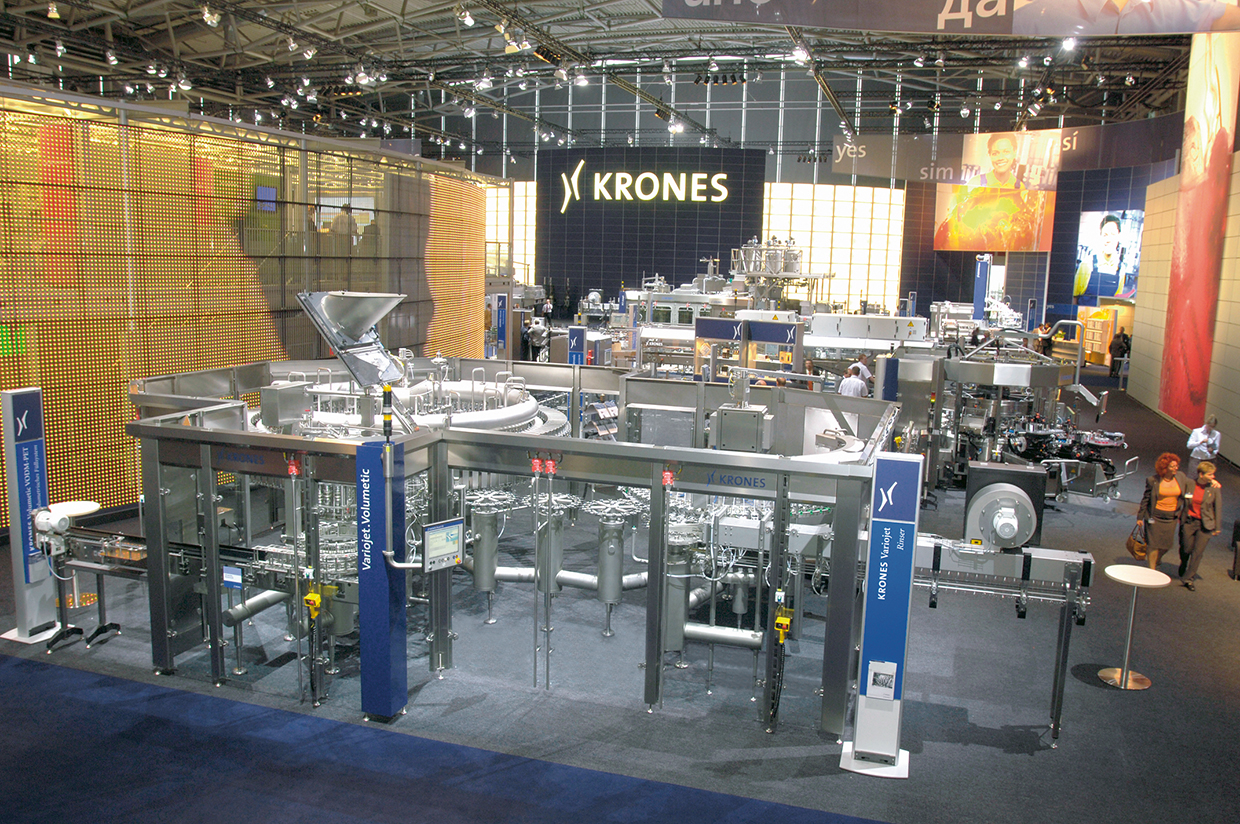
New types of drink added
In 2002, Krones got started in the field of milk filling, for which it introduced load cells. Milk foams when it is filled, which is why traditional fill-level measurement doesn’t work here. And milk’s conductivity is very low, so flow metering is not an option, either. That is why the fill quantity for milk is precisely determined by weighing.
2012 sees the introduction of the twin-flow system for juices with fruit chunks. In this system, juice and fruit chunks are heated up and filled separately. The FlexiFruit dosing system ensures that the exact amount of fruit particles is filled into the bottle.

Dynafill revolutionises the filling process
Up until the introduction of the Dynafill in 2017, the trade was convinced that carbonated beverages had to be filled under counterpressure because anything else would result in excessive foaming. “And then there was that colleague who said: That’s all way too slow,” recalls Matthias Wahl. The colleague had come up with the idea of filling a pressurised carbonated beverage into an evacuated bottle and applying the closure straight away without prior snifting.
That concept offers a whole lot of advantages: Beer’s oxygen pick-up is incredibly low, filling can take place without prior cooling, the fill level can be adjusted by means of pressure compensation between bottle and ring bowl, and since the bottles no longer have to travel from the filler to the closer being sprayed with water on their way, the risk of microbial contamination is significantly reduced. Thanks to warm filling, there is no more condensation downstream of the filler, so there is no need for a bottle warmer. Since there is no probe or vent tube involved, the entire diameter of the bottle mouth can be used, which makes for extremely fast filling. “A colleague had translated his idea into a laboratory set-up, and one fine day he showed it to me. That was in January 2014, I still remember it as if it was yesterday,” recalls Matthias Wahl. “Next day he presented the set-up to Volker Kronseder who said: Let’s do it.”
The Dynafill was presented at the drinktec 2017 where it demonstrated that beer bottles can be filled and crowned in less than five seconds – a new world record. “For Krones, that’s a unique selling point, we have very good patents protecting the system,” emphasises Matthias Wahl.
2017 also saw Krones transfer block technology to can filling and equip the Modulfill Bloc FS-C with a can seamer produced in-house.
The Dynafill – its details explained by two Krones colleagues who were involved in its development
100,000 PET bottles per hour
Krones set yet another milestone in 2022 – this time for performance in block technology, which we mentioned at the beginning of this article. The ErgoBloc L was the first block worldwide to boast an hourly output of over 100,000 PET bottles. The tricky spot in this context was the filler because the traditional approach of “a larger carousel equals higher performance” was limited by the laws of physics: Given the high speeds we’re talking here, the centrifugal forces would lead to the liquid level slanting in the bottles at the filler discharge, so product would spill over. This dilemma was solved by equipping the block with two modular filling and closing units, instead of just one giant carousel.
The Dynafill is also entering the next round: It uses artificial intelligence for the first time in 2024 for precise automatic adjustment of the fill level. As so many times before, this is yet another innovation made by Krones that is garnering attention in the sector – and it will certainly not be the last we’ve seen from them!